Monday, December 5, 2016
Fluid Power - Learn the Terminology
Burst Pressure - The pressure that causes rupture. Reference pressure intended for destructive testing purposes and design safety
factors only.
Fluid Power - Learn the Terminology
Buffing: The partial removal of the hose cover in order to put on a coupling. A stone wheel is
typically used to grind or buff the cover to remove the cover material.
Monday, November 7, 2016
Learn the Terminology
Cut-Off Length: The length of that part of the
coupling not directly in contact with or applied to the hose. Subtract the sum
of the cut-off length of the two couplings from the total length of the
assembly, and you will have the approximate hose-cut length to be replaced.
Dash Size: A shorthand method of denoting the size of a particular end
fitting or the inside diameter of a hose. Measured in 1/16 of an inch (i.e., -4 = 4/16”
or ¼”).Hose Cleanliness – Methods of measurement Part 2
There are three principal methods to measure
the contamination level in a component, circuit, or system:
1) Gravimetric Measurement (ISO 4405)
2) Particle Size Distribution Analysis (ISO 4406 or NAS 1638)
3) Maximum Particle Size Analysis (ISO 4407).
This post will discuss the second method (above).
Particle Size Distribution Analysis (ISO 4406 or NAS1638)
Particle Size Distribution Analysis is a reporting method to gauge both the size and number of contaminant particles in a calculated quantity of hydraulic fluid. A fluid sample is either taken directly out of a hydraulic system or a known quantity of fluid is used to dislodge contaminants out of a hydraulic component. This fluid is run through a particle counting instrument to size and count contaminant particles.
These particle ‘counts’ can then be normalized by comparing the total component volume and to a corresponding ISO 4406 ‘code’ level of particle contamination. Levels of five and 15 microns of contamination are reported on a logarithmic scale corresponding to and ISO 4406 ‘code’ for the number of particles greater than or equal to these respective sizes per milliliter of fluid.
1) Gravimetric Measurement (ISO 4405)
2) Particle Size Distribution Analysis (ISO 4406 or NAS 1638)
3) Maximum Particle Size Analysis (ISO 4407).
This post will discuss the second method (above).
Particle Size Distribution Analysis (ISO 4406 or NAS1638)
Particle Size Distribution Analysis is a reporting method to gauge both the size and number of contaminant particles in a calculated quantity of hydraulic fluid. A fluid sample is either taken directly out of a hydraulic system or a known quantity of fluid is used to dislodge contaminants out of a hydraulic component. This fluid is run through a particle counting instrument to size and count contaminant particles.
These particle ‘counts’ can then be normalized by comparing the total component volume and to a corresponding ISO 4406 ‘code’ level of particle contamination. Levels of five and 15 microns of contamination are reported on a logarithmic scale corresponding to and ISO 4406 ‘code’ for the number of particles greater than or equal to these respective sizes per milliliter of fluid.
Monday, October 24, 2016
Hose Cleanliness – affects Valves, Pumps, System cooling
Valves: Microscopic
contamination (similar to erosion) can mill away tolerances which are used for sealing
purposes. On spring centering valves, the debris may get caught between the valve and
the wall surface. The contamination will cause the slowing down of the motion
of the valve or causing sluggish or adverse mechanical actuation.
Abrasive
particles enter the clearances between moving parts they score and hone the surfaces
to greater tolerances. As these tolerances broaden, system performance is
compromised by pressure losses incurred due to fluid leakage from high to lower
pressures.
The worst
occurrence is when particles that are greater than or equal in size to
the orifice openings become wedged between the two surfaces. The
contamination may cause wear to occur or it may cause the system components to
seize.
Pumps &
drives: Microscopic contamination can mill
away material, creating leak points. These leak points rob the hydraulic system
of pressure and cause poor responsiveness.
System
cooling: Working fluid may not flow through to remove contaminants generated
from metal to metal contact when passages
become blocked. Lower flow rates mean greater heat buildup in systems and
thermal breakdown of the working fluid.
Hose Cleanliness - Origin of Contamination
Origins of
contamination may be from system components, the
hydraulic working fluid, the outside environment, or be generated by the system itself.
These contaminants, some large and some microscopic, can have a profound impact
on the performance and longevity of the hydraulic system.
There are
three principal means through which contamination can
occur in a
typical hydraulic system.
Contamination
can be:
1. Generated
during system operation
2. Built
into the system during assembly
3. Ingested by the system during operation
Monday, October 17, 2016
Blast from the Past
Tuesday, October 4, 2016
Learn the Terminology - Fluid Power
Compressibility: The change in volume of a unit volume of a fluid
when subjected to a unit change of pressure.
Contaminant: Any material or substance that is unwanted or
adversely affects the fluid power system or components or both.
Corrosion: The chemical change in the mechanical elements caused by
the interaction of fluid or contaminants or both. More specifically related to
chemical changes in metals.
The products of change may be introduced into the system as generated
particulate contamination.
Wednesday, September 7, 2016
Fluid Power: Learn the Terminology - Cavitation
Cavitation: A localized gaseous condition within a liquid
stream causing the rapid implosion of a gaseous bubble.
Tuesday, September 6, 2016
Belt Storage Recommendations
In order to retain their serviceability and dimensions, proper storage procedures must be followed for power transmission belts. Quite often, premature belt failures can be traced to improper belt storage procedures that damaged the belt before it was installed on the drive. By following a few guidelines, these types of belt failures can be avoided.
Belts should be stored in a cool and dry environment with no direct sunlight. Ideally, belts should be stored in an environment that is less than 85 degrees F and with lower than 70% relative humidity.
Do not store where the belts are exposed to direct sunlight or moisture.
Do not store near heaters, radiators, or heating devices.
Do not store near ozone generating devices such as transformers or electric motors.
Do not store belts where they can be exposed to solvents or chemicals.
Do not store in locations where the belts are exposed to traffic that may cause damage.
Do not crimp belts during handling or while being stored.
Do not bend to diameters smaller than the minimum recommended diameter for the belt cross section.
Do not use ties or tape to pull belt spans tightly together near the end of the belt.
Do not hang on a small diameter pin or nail that suspends all of the belt weight and bends the belt to a diameter smaller than the minimum recommended diameter.
Belts should be stored in a cool and dry environment with no direct sunlight. Ideally, belts should be stored in an environment that is less than 85 degrees F and with lower than 70% relative humidity.
Do not store where the belts are exposed to direct sunlight or moisture.
Do not store near heaters, radiators, or heating devices.
Do not store near ozone generating devices such as transformers or electric motors.
Do not store belts where they can be exposed to solvents or chemicals.
Do not store in locations where the belts are exposed to traffic that may cause damage.
Do not crimp belts during handling or while being stored.
Do not bend to diameters smaller than the minimum recommended diameter for the belt cross section.
Do not use ties or tape to pull belt spans tightly together near the end of the belt.
Do not hang on a small diameter pin or nail that suspends all of the belt weight and bends the belt to a diameter smaller than the minimum recommended diameter.
Tuesday, August 30, 2016
Contacting Product Application
If you have questions on any technical subject regarding industrial belts, industrial hose or hydraulic hose, Gates Product Application Engineering is available to help!
Product Application engineers can provide technical recommendations on material compatibility, connectors, drive design, troubleshooting, and belt drive analysis.
You can contact us by either phone or email:
Industrial Belts:
Phone: 303-744-5800
Email: PTPASupport@gates.com
Industrial Hose, Hydraulic Hose:
Phone: 303-744-5070
Email: FPPASupport@gates.com
Product Application engineers can provide technical recommendations on material compatibility, connectors, drive design, troubleshooting, and belt drive analysis.
You can contact us by either phone or email:
Industrial Belts:
Phone: 303-744-5800
Email: PTPASupport@gates.com
Industrial Hose, Hydraulic Hose:
Phone: 303-744-5070
Email: FPPASupport@gates.com
Monday, August 22, 2016
Poly Chain in the Winner's Circle!
Gates Poly Chain belts are used to power the superchargers in the Top Fuel and Funny Car categories in the NHRA. The blower belt is subjected to loads of over 1000 HP, and explosive and damaging torque reversals in every run. Gates belts have been used for decades, and lead the way with new technology for the application.
Gates sponsors John Force Racing, the legendary team led by John Force. The most recent race, the Lucas Oil Nationals in Brainerd, MN saw strong performances by all of the team's cars, but in particular a win in the Top Fuel category by Brittany Force driving the Monster Energy Top Fuel Car. Brittany made it through a tough field to beat 2 time Top Fuel champion Antron Brown in the final round.
The win is Brittany's third of the 2016 season, placing her 4th place for the season in points.
Gates is proud to sponsor John Force Racing in their chase for the title!
Gates sponsors John Force Racing, the legendary team led by John Force. The most recent race, the Lucas Oil Nationals in Brainerd, MN saw strong performances by all of the team's cars, but in particular a win in the Top Fuel category by Brittany Force driving the Monster Energy Top Fuel Car. Brittany made it through a tough field to beat 2 time Top Fuel champion Antron Brown in the final round.
The win is Brittany's third of the 2016 season, placing her 4th place for the season in points.
Gates is proud to sponsor John Force Racing in their chase for the title!
Tuesday, August 16, 2016
FDA Belting
Have you ever found yourself in need of a synchronous belt to be used in a area that needs a special, FDA construction? Look not further. Gates offers a construction option that will meet your FDA needs. This FDA construction option is intended for use in applications where a food-grade belt construction is required. These belts are a yellowish-tan, non-marking Duro 52 with a special non-coated jacket and are ideal for food conveyors, washdown applications and anti-bacterial conveyors.
Please note: Gates synchronous belts have been used extensively throughout the food and beverage industry in applications where the belts do not directly contact food.
While the FDA
does not either approve or disapprove of the use of belts in food-related
application, they have identified certain materials or ingredients that have
been approved. Gates special yellow rubber compound specifically meets those
FDA requirements regarding materials and ingredients.
The USDA will evaluate and
approve belts on an individual basis if submitted to them. Gates has not
requested any USDA approvals. If the USDA belt approval is required, then the belt user should submit specific belt samples directly to the USDA.
For additional information on this or any other topic please contact Gates Product Application Engineering by phone at 303-744-5800
or by email at ptpasupport@gates.com.
Monday, July 25, 2016
Quick-Link - Gates Emergency V-belt Solution
Unplanned drive downtime can be expensive. However, stocking numerous replacement belt sizes can also be costly. The Gates Quick-Link V-belt offers an alternative. It can be quickly assembled by hand into whatever length you need.
Quick-Link is available in the following sizes:
For a demonstration of the assembly process, watch our latest video:
Quick-Link
Quick-Link is available in the following sizes:
For a demonstration of the assembly process, watch our latest video:
Quick-Link
Labels:
belt replacement,
Quick-Link,
V-belt,
V-belt drives,
V-belts
Tuesday, July 19, 2016
Rim Speed Limits For Sheaves / Pulleys / Sprockets
Belt drive hardware has rotational
speed limits in order to prevent excessive hoop stress levels that could result
in physical material failures. Material
failures can be catastrophic with fragments thrown outward at high velocities and
energy levels, so speed limits should not be exceeded.
Speed limits are based on the hardware material, as well as
on the hardware configuration. Block
style hardware is inherently stronger than hardware with rims or spokes, so can
operate at higher speeds.
Rotational speed limits are most commonly expressed in terms
of rim speeds. Common units used to
express rim speed are feet per minute (ft/min) and meters per second (m/s). Maximum rpm limits can be calculated from rim
speeds with hardware diameters known. An
equation to calculate hardware rpm from rim speed is as follows:
RPM = (Rim Speed (ft/min) x 3.82)/Diameter (in)
A table from the Mechanical Power Transmission Association
Standard B13i-2013 containing rim speed limits for a variety of hardware
configurations and materials is as follows:
Belt drive hardware is often stamped with maximum rpm values,
and will likely be based on this data.
Tuesday, July 12, 2016
Will It Fit - Poly Chain GT2 Sprockets
What belt
will fit into what industry standard sprocket is a question we regularly
receive here in Product Application. Below is information regarding what
Gates belts will fit into standard Poly Chain GT2 sprockets.
**When designing belt drives for NEW APPLICATIONS with Poly Chain GT Carbon power ratings: DO NOT use Poly Chain GT sprocket systems. Poly Chain GT sprockets/bushings may not handle the increased torque load capacity and damage to the sprocket and/or bushing may occur. ONLY use Poly Chain GT2 sprockets for new designs.**
For any additional questions, feel free to contact us at PTPASupport@gates.com or 303-744-5800.
Tuesday, June 21, 2016
Understanding V-belt Construction Terms
V-belt construction features can be described by a variety of terms, which can cause confusion. Here are some of the most common terms you may encounter:
- Banded:
- A fabric layer surrounds the belt
- Also referred to as wrapped or covered
- Bareback:
- A type of banded V-belt where the fabric is not impregnated with rubber
- Also referred to as low friction, dry cover, or clutching cover
- Bandless:
- No fabric surrounding the belt
- Also referred to as cut edge, raw edge, or machined edge
- Notched:
- The bottom of the belt is notched (not flat)
- Also referred to as cogged, molded notch, or cut notch
- PowerBand®:
- Multiple V-belt strands joined with a common backing
- Also referred to as joined
Wednesday, June 8, 2016
Interchanging OEM Original Equipment V-belts With Standard Aftermarket V-belts
V-belts are commonly used in many
light duty type applications including outdoor power equipment (lawn mowers,
rotor tillers, snow blowers, etc.), light duty ventilation fans, power tools
(table saws, drill presses, wood lathes, etc.) and much more. V-belts eventually need to be replaced, and
obtaining appropriate replacements can be challenging.
OEM Originals
Replacement belts can nearly
always be obtained from the original equipment manufacturers, and this is usually
the best practice. OEM Manufacturers
often use belts that have been custom manufactured for them in special
constructions or in custom lengths that function best in their equipment. These special constructions are proprietary,
so the special features may not be easily determined.
Truflex and PowerRated Replacements
If original OEM V-belts cannot be
obtained, replacement belts can sometimes be identified dimensionally although
performance and functionality may not be the same as the OEM originals. When considering replacement belts from our
Truflex and PowerRated light duty V-belt product lines, there are additional considerations.
Clutching Applications
Clutching Applications
Some applications use belts to
provide a clutching function to engage and disengage the equipment. Only PowerRated type V-belts should be used in
these applications as they have been designed with a bareback type cover that
allows graceful slippage and aramid tensile cords that will not shrink like
Truflex V-belts when hot from slippage.
Using conventional Truflex V-belts could cause unsafe machinery
engagement and belt shrinkage could prevent disengagement, resulting in
potentially hazardous circumstances.
V-belt Length Variations
Standard Truflex and PowerRated
V-belts may not fit applications like OEM originals. Standard V-belts may be too short to easily
install or too long, resulting in adjustment pulleys moving to the end of their
travel and not able to apply sufficient belt installation tension. The position of spring loaded tensioning
pulleys may also change, resulting in an increase of decrease in the proper
belt tension.
PowerRated For Increased Robustness
Identically sized PowerRated V-belts
can sometimes be used in place of Truflex V-belts for added load capacity and
robustness. This can sometimes improve
belt service life when Truflex V-belt performance is less than desired. Truflex V-belts should generally not be
substituted for PowerRated V-belts, though.
Interchanging with Industrial V-belts
Identically sized Industrial
A-Section and B-Section V-belts can sometimes be used in place of Truflex
V-belts for added load capacity and durability.
Note, however, that small sheave diameters often used in these
applications may be too small for solid banded A-Section and B-Section
V-belts. AX-Section and BX-Section
(notched) V-belts are more flexible and tolerant of small sheave diameters, so
may perform better.
Summary
Identifying correct replacement belts for equipment can be challenging. We recommend that you consult original equipment manufacturers first for the best replacement. Then consider the functionality needed by the belt in selecting V-belts from our standard product lines. Contact Gates Product Application Engineering for further information at 303.744.5800 or ptpasupport@gates.com.
Identifying correct replacement belts for equipment can be challenging. We recommend that you consult original equipment manufacturers first for the best replacement. Then consider the functionality needed by the belt in selecting V-belts from our standard product lines. Contact Gates Product Application Engineering for further information at 303.744.5800 or ptpasupport@gates.com.
Tuesday, May 31, 2016
Will It Fit - GT2 Sprockets
What belt will fit into what industry standard sprocket is a question we regularly receive here in Product Application Engineering. Below is information regarding what Gates belts will fit into standard PowerGrip GT2 sprockets.
For any
additional questions feel free to look through our other blog topics or contact
us at ptpasupport@gates.com or
303-744-5800.
Minimizing V-belt Drive Noise
To minimize the noise level of your V-belt drive, pay close attention to tension and alignment.
Improper V-belt tension can cause the belt to slip and squeal. Misalignment creates interference at the belt’s entry point into the sheave, resulting in a louder drive.
Information on proper belt installation tension and alignment is detailed in the V-belt manual:
HEAVY-DUTY V-BELT DRIVE DESIGN MANUAL
Improper V-belt tension can cause the belt to slip and squeal. Misalignment creates interference at the belt’s entry point into the sheave, resulting in a louder drive.
Information on proper belt installation tension and alignment is detailed in the V-belt manual:
HEAVY-DUTY V-BELT DRIVE DESIGN MANUAL
Wednesday, May 4, 2016
Hose Cleanliness
Hose Cleanliness
When the
customer becomes more dependent on ISO standards, your
strategy needs to reflect a dedication to system
cleanliness.
What is
Hydraulic System Cleanliness?
liquid contamination found in hydraulic systems. “Contamination”
is defined
as any substance that is not part of the hydraulic system’s
working
fluid.
Why is
cleanliness important to your
customers?
There are several reasons:
Improved
control - spare
parts use can be controlled through preventive maintenance and
monitoring contamination.
Reduce
equipment downtime - through
scheduled inspections
failure for
increased life expectancy of components on equipment.
Reduced
repair cost - due
to fewer breakdowns.
Several
reputable sources have claimed that 70 to 80 percent of
hydraulic
system failures are due to contamination. By establishing
a contamination
control program, costly repairs and downtime may
be
minimized. A contamination control
program can be as simple
as
establishing an allowable level of contamination within a hydraulic
system,
supplying cleaned components for the system, and monitoring
levels of
contamination as part of a preventive maintenance
program.
Wednesday, April 27, 2016
Metric V-belt Lengths
Depending on the belt type and the manufacturer, metric V-Belt part number may specify different length measurements. The different belt lengths, abbreviations, and their relative positions in the belt are:
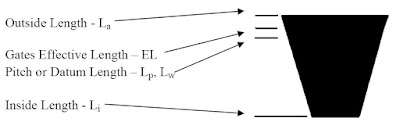
Gates classical Metric Power™ V-belts (e.g 10X, 13X, 17X) specify inside length in millimeters followed by”Li”. Narrow Gates Metric Power V-belts (e.g. SPZ, SPA, SPB, SPC) specify the datum/pitch length in millimeters.
Converting one length type into another may be required to identify if a proper replacement belt exists. The following table converts between any of the four length measurements. To find the correct equation, read the column headings across the top and choose the appropriate belt cross section. Read down the rows at the left and select the belt length type to calculate. Reading down the selected column and across the selected row, the box at the intersection lists the equations to convert from any of the other three length types.
Gates classical Metric Power™ V-belts (e.g 10X, 13X, 17X) specify inside length in millimeters followed by”Li”. Narrow Gates Metric Power V-belts (e.g. SPZ, SPA, SPB, SPC) specify the datum/pitch length in millimeters.
Converting one length type into another may be required to identify if a proper replacement belt exists. The following table converts between any of the four length measurements. To find the correct equation, read the column headings across the top and choose the appropriate belt cross section. Read down the rows at the left and select the belt length type to calculate. Reading down the selected column and across the selected row, the box at the intersection lists the equations to convert from any of the other three length types.
Tuesday, April 26, 2016
Using Extra Wide Driven Sprockets and Sheaves to Increase Bore Ranges
Hardware component selections for normal belt drives use the
same widths for both the driver and driven sprockets or sheaves. This
looks normal and works well most of the time.
But what if the driven shaft diameter is unusually large and
exceeds the bore range of the selected driven sprocket or sheave? One option is to re-design and select
hardware components with larger bore ranges.
Another option is to consider using a driven component in the same
diameter, but in a wider width than necessary.
For example, an 8MX-140S-12 sprocket uses a 2012 bushing
with a maximum bore of 2.125”. An
8MX-140S-21 sprocket uses a 2517 bushing with a maximum bore of 2.688”. In this case, just using a sprocket with a 21mm
face width instead of a 12mm face width will increase the sprocket bore range from
2.125” to 2.688”, which is considerable.
This principle can apply to other sprocket, pulley and sheave types as
well.
With synchronous belt drives there is no harm in using wider
driven sprockets so long as the driver sprocket is double flanged so the belt
is constrained appropriately on both sides.
A wider driven sprocket may look unusual, but will function just
fine. And the parallel sprocket
alignment isn’t as critical with the wider sprocket face width.
With V-belt drives there is no harm in using wider driven
sheaves. There may be some empty sheave
grooves in the wider driven sheave, but this will not pose any problems. Just be sure to accurately align the driver
sheave grooves with the driven sheave grooves that will contain V-belts.
For questions or further information, contact Gates Product
Application Engineering at 303-744-5800 or at ptpasupport@gates.com
Friday, April 15, 2016
Will It Fit - HTD Sprockets
What belt will fit into what industry standard sprocket is a question we regularly receive here in Product Application. Below is information regarding what Gates belts will fit into standard HTD sprockets.
** Please note: When designing belt drives for new applications with PowerGrip GT3 power raitings, DO NOT use HTD sprocket systems. HTD sprockets and bushings may not be able to handle the increased torque loads and damage to the sprocket and/or bushing may occur. Only Use PowerGrip GT2 sprockets for new PowerGrip GT2 designs.**
** Please note: When designing belt drives for new applications with PowerGrip GT3 power raitings, DO NOT use HTD sprocket systems. HTD sprockets and bushings may not be able to handle the increased torque loads and damage to the sprocket and/or bushing may occur. Only Use PowerGrip GT2 sprockets for new PowerGrip GT2 designs.**
For any additional questions feel free to look through our other blog topics or contact us at ptpasupport@gates.com or 303-744-5800.
Monday, April 4, 2016
Get Your Career Spinning - Gates PT Workshop
We are pleased to announce that Gates now offers power transmission workshops for customers and distributors. Over a two day period our product application team instructs students on the following topics:
Gates Products Overview
Belt Drive Design Basics
Roller Chain Conversions
Energy and Maintenance Savings
Drive Inspection and Troubleshooting
Drive Installation
And more!
For more information and registration please visit http://cms.gates.com/gatesu/home
Tuesday, March 15, 2016
New Configuration For Gates EZ Align Green®
Gates EZ Align™ laser alignment tools are the best available. Aside from their exceptional durability and robustness,
the reflected beam technology magnifies detected shaft angularity for much more
accurate detection than other tools.
While
original EZ Align units used a red laser, an improved EZ Align Green model was introduced few years ago.
![]() |
Original EZ Align Green |
EZ Align Green uses a powerful green laser that is 20X brighter than the standard red laser. The increased power and green color make it readily visible in daylight and increase the range from about 6 feet to 15 feet or better.
The original
EZ Align Green units emitted the laser beam from the end of the
transmitter as seen in the illustration at left. This was a different configuration than standard EZ Align Red units.
Improvements in laser technology and size now allow the green laser beam to be emitted from the side of the transmitter, like the standard EZ Align Red units.
![]() |
New EZ Align Green Configuration |
Now EZ Align Red and EZ Align Green units use identical configurations for convenience and easier use.
For further information, contact Gates Product Application
Engineering at 303-744-5800 or at ptpasupport@gates.com.
Friday, March 11, 2016
Product Application Engineers on YouTube
Are you looking for an easy way to learn more about Gates belts and hoses?
Head over to www.YouTube.com/GatesPT/ for videos created by the Product Application Engineering team.
Once on the site, navigate to the Learn with the Gates Product Application Team and Lessons from Gates Professionals play lists to get quick access to the engineer's videos. Recent additions include topics such as:
Feel free to contact us at ptpasupport@gates.com or +1.303.744.5800 if you have any additional questions.
Head over to www.YouTube.com/GatesPT/ for videos created by the Product Application Engineering team.
Once on the site, navigate to the Learn with the Gates Product Application Team and Lessons from Gates Professionals play lists to get quick access to the engineer's videos. Recent additions include topics such as:
- TaperLock Bushing Installation
- QD Bushing Installation
- Gates Super HC XP belts
- eCrimp
- Gates Mectrol – Specialty Belts
Feel free to contact us at ptpasupport@gates.com or +1.303.744.5800 if you have any additional questions.
Wednesday, March 2, 2016
2016 NHRA Season is Underway!
The 2016 NHRA Drag Racing season has begun and whether you are a fan or not, it is hard to not be in awe when watching two 10,000 horsepower cars racing down a 1,000 foot track. These nitro-fed engines are some of the harshest applications imaginable and the professionals rely solely on our Poly Chain supercharger belts to power them to the winners circle. The performance of our premium belting in these application is a testament to the technology and innovation Gates brings to all of our products. From 10,000 horsepower Top Fuel Funny Cars and Dragsters to 1/4 horsepower precision timing application, Gates has the right product for the job.
Gates is a proud sponsor of the John Force Racing team and wishes them the best of luck in their 2016 campaigns. CLICK HERE to hear about the quality of Gates products directly from the John Force Racing team.
Gates is a proud sponsor of the John Force Racing team and wishes them the best of luck in their 2016 campaigns. CLICK HERE to hear about the quality of Gates products directly from the John Force Racing team.
Tuesday, February 16, 2016
Which Sprockets Have Flanges?
If you've read the blog post on flanged sprockets then you're aware that not all sprockets have flanges. Most applications only need flanges on one sprocket. For this reason larger sprockets don't have flanges. The table below shows the number of grooves in the largest standard sprocket with flanges. Any standard sprocket with more teeth will not have flanges.
Sprocket details may change without notification.
Wednesday, February 3, 2016
Easy Fixes For Obtaining Readings From Gates 508C Sonic Tension Meter
The new Gates 508C Sonic Tension Meter is an excellent tool,
and is very easy to use. Occasional user
difficulties often result from some common issues. Solutions to a couple of common issues
follow.
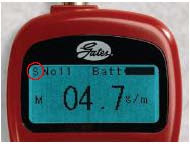
Change the frequency mode by holding the “Range” key down (zero button) until the screen changes. Then toggle to select the “Standard” range with the “up” (8 button) and “down” (2 button) keys. Press “Measure” afterward to return to the main screen and look for the “S” in the upper left hand corner of the screen.
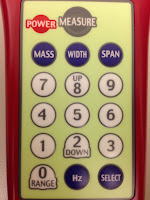
Many users prefer the simplicity of span frequency, but don’t
know whether the “Mass”, “Width” and “Span” constants need to be entered. The constants do not effect belt span
frequency measurements, but incorrect constants can result in a meter display
overflow, or “Error Re-Measure” message.
If the meter is to be used to measure belt span frequencies
only, here’s a really handy trick. Enter
values of 1.0 for all three constants. Now
the meter will display zero tension, but press the “Hz” button for the
frequency display mode. Now the meter
will display accurate belt span frequency values, not display belt tension, and
not display an error message from incorrect constants.
Contact Product Application Engineering at 303-744-5800 or at ptpasupport@gates.com for further assistance with Gates Sonic Tension Meters.
Wednesday, January 27, 2016
Selecting Batteries for the Sonic Tension Meter 508C
For optimum meter performance, use two disposable AAA
alkaline batteries.
Gates’ 508C Sonic Tension Meter is designed to use two AAA alkaline
batteries, rated for 1.5 volts each (3.0 volts combined). When used with new alkaline batteries, the
estimated continuous use time is 10 hours. Using other battery types, such as lithium
ion (Li-Ion) or nickel cadmium (NiCd), may reduce the meter run time.
Note: The information in this blog post also applies to the older 507C model.
Wednesday, January 20, 2016
Sprocket and Sheave Balancing
Stock sprockets and sheaves are statically balanced per MPTA ( Mechanical Power Transmission Association) Standard Practice for Pulley Balancing SPB-86 using the weight based on the following two criteria:
1. Balance limit (ounces) = Sprocket Weight (lb) x 0.016; or
2. 0.176 ounce (5 grams), whichever is greater
It is important to note that stock sprockets and sheaves should not be used on drives where the rim surface speeds exceed 6500 fpm. Sprocket and sheave construction and materials will determine the dynamic balancing requirements of the sprocket(s) or sheave(s) where rim surface speeds exceed 6500 fpm.
If rim speed exceeds 6500 fpm, then the sprocket(s) or sheave(s) will need to be quoted through our Made-to-Order Metals group. They can be contacted directly at makemymetal@gates.com or 800-709-6001 however any quotes will need to be made through your local Gates industrial belt distributor.
For any additional questions feel free to look through our other blog topics or contact us at ptpasupport@gates.com or 303-744-5800.
1. Balance limit (ounces) = Sprocket Weight (lb) x 0.016; or
2. 0.176 ounce (5 grams), whichever is greater
It is important to note that stock sprockets and sheaves should not be used on drives where the rim surface speeds exceed 6500 fpm. Sprocket and sheave construction and materials will determine the dynamic balancing requirements of the sprocket(s) or sheave(s) where rim surface speeds exceed 6500 fpm.
If rim speed exceeds 6500 fpm, then the sprocket(s) or sheave(s) will need to be quoted through our Made-to-Order Metals group. They can be contacted directly at makemymetal@gates.com or 800-709-6001 however any quotes will need to be made through your local Gates industrial belt distributor.
For any additional questions feel free to look through our other blog topics or contact us at ptpasupport@gates.com or 303-744-5800.
Friday, January 15, 2016
Drive Conversion Worksheet
Are your drives dragging you down?
Use the Gates Drive Conversion Worksheet. Let us Engineers do the work for you.
If out-of-date drive systems are dragging you down, consider converting to a belt drive system that maximizes your application and output.
Complete our Drive Conversion Worksheet and a Gates product Engineer will provide you with a custom belt drive system recommendation. It’s a no-brainer for saving money, reducing downtime, and improving efficiency.
Use the Gates Drive Conversion Worksheet. Let us Engineers do the work for you.
If out-of-date drive systems are dragging you down, consider converting to a belt drive system that maximizes your application and output.
Complete our Drive Conversion Worksheet and a Gates product Engineer will provide you with a custom belt drive system recommendation. It’s a no-brainer for saving money, reducing downtime, and improving efficiency.
LAUNCH THE WORKSHEET | ![]() |
Monday, January 4, 2016
Hydraulic Fluid Properties
Lubricity – the fluid must keep friction low and
maintain an adequate film between moving parts to prevent wear of pumps,
bearings, vanes, gears, pistons and rods. Increasing pressures and, consequently, closer tolerances, make
lubricity even more important.
Viscosity – fluid “thickness” or resistance to flow. Pump manufacturers
specify this according to clearances, speeds, temperatures and suction characteristics.
The fluid must be thin enough to flow freely, yet heavy enough to prevent wear and
leakage. Viscosity might not be so critical in selecting a hydraulic fluid except that it varies with temperature. Fluid
thickens when it cools, thins as it heats up. Because some hydraulic systems
must work under wide temperature extremes, viscosity range is important.
Viscosity Index – This measures the rate of viscosity change with temperature: the
higher the index, the more stable the viscosity as temperature varies.
Subscribe to:
Posts (Atom)